Unintended consequences are everywhere. Everyday actions, as well as design considerations, often precipitate other actions that were not planned or expected. Such seems to be the case with current-technology automotive fuel injection systems.
Induction systems have evolved from relatively crude early carburetors to the mechanical fuel injection systems of the 1950s to electronic throttle body injection to port injection to today’s gasoline direct injection (GDI) systems. And while these new systems set new standards for performance, fuel economy and emission control, alas they do come with unintended consequences. The most notable of these is the formation of carbon deposits on the backs of intake valves.
Direct injection means that, unlike port injection, which sprays fuel into intake ports just upstream of the intake valves, fuel is instead sprayed directly into the combustion chamber. With precise spray patterns, atomization is virtually instantaneous, such that the combustion process is optimized. Similar technology is used in today’s diesel engines.
But this is where the unintended consequences raise their ugly head. Remember, crankcase ventilation systems collect crankcase and blow-by gases and route them through the induction system to be burned off before they can exit the tailpipe and contribute to air pollution.
With the earlier port injection systems, fuel was sprayed at the backs of the intake valves on its way into the combustion chamber. This near-constant spraying of fuel cooled the intake valves and helped to wash away deposits that would otherwise form. With direct injection, this cooling effect is lost, and the result is intake valves that run far hotter than ever before. The unintended consequence is that oily crankcase vapors being drawn past the intake valves tend to collect and cook on the backsides of the hot intake valves.
These deposits are no friend of the engine. The accumulation of these deposits can become quite substantial and can greatly affect the incoming air charge, reducing the amount of air drawn in on the intake stroke and also causing turbulence that can compromise atomization and efficiency. Such turbulence and obstruction are the reasons racers port and polish cylinder heads for competition — to optimize the speed and volume of the incoming (and outgoing) gases.
In extreme cases, deposits on intake valves must be removed mechanically. There are systems that involve partial engine disassembly and, after much preparation, blasting away these deposits with walnut shells or other blasting media. In some cases, it can be necessary to remove the cylinder head(s) for valve service at a capable machine shop. But both of these approaches are costly and time-consuming — and are not particularly well-suited to the quick lube environment.
Fortunately, there are chemical products that can perform the cleaning task very well. Carefully-blended fuel system additives can be very effective in removing the carbon deposits on intake valves. They can include specially-formulated detergents and solvents crafted for this specific task. Such additives represent a natural add-on sale for the quick lube shop, particularly if the shop keeps a couple of heavily-carboned valves on hand to provide a powerful demonstration for the customer.
Such proprietary blends include additives that provide enhanced lubricity and corrosion protection throughout the fuel system, as well as anti-oxidants that promote fuel stability. This is especially critical with today’s ethanol fuels.
An added benefit of such products is that their cleansing properties also help to purge contaminants from the entire fuel system. This is particularly critical with GDI engines, in which the fuel injectors have very tiny orifices and spray patterns are critical. Any debris that compromises the fuel delivery in any way can have a serious impact on engine performance and fuel economy.
A more ambitious cleaning can be performed with professional-quality multi-part chemical cleaning systems. Such special service kits include one product that is introduced into the induction system via the throttle body or fuel rail. This provides a direct and powerful softening and removal of intake valve deposits. A second step involves the addition of a different product that is added to the fuel tank. This product provides final cleaning and on-going protection against future build-ups.
Vehicles can be serviced using these professional service kits in a relatively short period of time, making them a viable service for the quick lube environment. It also provides the opportunity for continued sales of fuel tank additives, so customers can help prevent future carbon build-up problems.
Savvy quick lube operators are always on the lookout for value-added products and services that can be performed quickly and profitably while providing excellent value for the customer. GDI service, on both gasoline and diesel-powered cars and light trucks, represents such a service without the need for special training nor the need to stock multiple SKUs in order to accommodate popular makes and models.
The resulting added business can be a very intended consequence.
About the Author
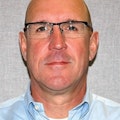