An automotive service facility’s staff can do far more than provide excellent maintenance that impacts individual customers on one day. If they receive professional training and experience consistent teamwork, they will develop the expertise and confidence to notice and understand risks before they turn into lasting problems. Among those risks are consumers’ misunderstanding of the maintenance requirements in owner's manuals and automobile manufacturing and design defects typically blamed on unsuspecting aftermarket service providers. From the greeter to the lower bay technician, everyone has an important role to play in creating a team that supports both their shops and long-term customer success.
Ask the Important Questions
One question in particular often gets overlooked and unnoted on receipts. When the customer is a first-time patron, ask about their last oil change interval. If you think it doesn’t matter because they’re new to you, think again. Many, if not most, consumers don’t understand the importance of OEM recommended owner’s maintenance schedules or what the terms mean. They don’t realize that automakers have a history of refusing to honor engine warranties for failure to get oil changes and other services within the recommended service intervals. For oil changes, those intervals tend to run from 3,000 to 5,000 miles for “severe” driving conditions. Here’s a translation for anyone not steeped in OEM-speak: The most common driving conditions, which should be named “normal,” are nevertheless misnamed “severe” by automakers.
A consumer who drives like everyone else in their community will likely consider themselves to be driving normally no matter what the conditions and choose the “normal” A.K.A. longest service interval. The normal/longest service interval also tends to be the one advertised when consumers go shopping for a new vehicle. See why your new customers might be confused? And if they have been confused, they may have even exceeded the normal/longest service interval. That would mean their OEM engine warranty is likely shot before anyone from your facility touched the vehicle. Find out the service history, make a note of it, offer the customer some quick education if they need it, and request the customer sign a disclaimer if you need it.
Recognize Odd Parts
Innovation can move the automotive industry forward, but it can also fail miserably. Oil drain pans and drain plugs, for example, are usually made of steel. However, a few automakers decided to try plastic composite drain pans, at least one of them comes with a plastic drain plug, and all of it has been problematic to service (see more below). Another plastic problem comes from skid plate fasteners. Again, it’s odd to see plastic used in situations where it is likely to snap during service and/or become brittle via exposure to the elements. Yet another odd plastic part is the late model Hyundai/Kia plastic oil filter cannister with its tiny, troublesome oil drain plug. DIYers and other vehicle service providers may also swap out original parts for non-specification parts, which can impact the service procedure. It’s important to recognize when parts involved in requested service are odd, make a note of it, snap a pic, and seek clarification on service procedures.
Know Potential Defect Symptoms
The work I do with the Preventative Automotive Maintenance Association (PAMA) involves cutting edge vehicle defect detection made possible by unprecedented industry and consumer participation. Anyone who does not want to pay for OEM defects often knee-jerk blamed on the last service provider would be wise to join PAMA today, if they’re not members already, and make sure to receive the monthly Government Affairs Update. One of the current investigations is focused on 2022-2023 Nissan Rogue with the 1.5L KR15DDT engine. It has a plastic composite oil drain pan with a drain plug that falls out, threads unit and all, most often when someone simply tries to loosen the drain plug for an oil change. Plop. At that point, there’s not much to be done except replace the entire drain pan and they’re reportedly out of stock across much of North America.
Nissan issued a Technical Service Bulletin (TSB) for the 2022 Nissan Rogue with the 1.5L engine directing the use of no more than 25 ft-lbs of torque pressure to tighten the drain plug, which is 2 ft-lbs less than the recommendation in the owner’s manual and printed on the oil drain pan itself. Based on the current record of complaints, Nissan’s TSB isn’t solving the problem. Some service providers have already switched to extraction-only for those Nissan models. Other common, potential defect symptoms include customers arriving with no oil on the dipstick (excessive oil consumption), loose oil drain plugs (oil drain pan defect), and, of course, engine knock (often a connecting rod bearing defect). Whatever potential defect symptom is found, make a note of it, and seek clarification on service procedures.
Write it Down for the Record
It doesn’t help anyone if a greeter or service technician identifies a problem, but no one makes a note of it on the customer’s invoice. That document, whether hard copy or digital, is the primary record of the vehicle’s condition at the time of service. The same information on receipts usually gets retained in the shop’s software so make the most of that resource. Moreover, engine defects blamed on the last service provider’s service are harder to defend without it. Do yourself and your customers a favor by memorializing your staff’s super sleuth powers of trained observation.
About the Author
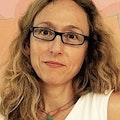
Joanna Johnson
Joanna L. Johnson, Esq., is the President of Johnson Policy Associates, Inc., a firm specializing in federal and state regulation of automotive repair, unfair and deceptive practices, environmental, transportation, competition, and workplace safety. Formerly a partner in the law firm of Harris, Johnson & Stonecipher in Bozeman, Montana, which specialized in federal regulation and legislation, she started her career in Washington, D.C. as in-house counsel for multi-national trade associations. She also created and ran the government affairs program, including the Government Affairs Update, for the Preventative Automotive Maintenance Association (formerly AOCA), serving as general counsel and then government affairs policy advisor for several decades.