No claims today. I mentally say that to myself every morning. It is the goal I set for my crews every morning. I mention the basics every time: Don’t get in a hurry and take shortcuts. Don’t let the circumstances or customers rush you out of your comfort zone. Pay attention to everything you are doing on each vehicle, and follow every safety procedure on every vehicle.
I am lucky. My shops do not suffer with an inordinate amount of claims, but I would definitely say luck has much to do with it. Following procedures and keeping those thoughts in the forefront of all my employees’ minds on a daily basis is largely where that situation comes from.
Claims come from several sources. Of course, claims arise from mistakes made during the service of the vehicle. These can be decreased by strict adherence to service procedures. Then, there are the claims that come from the “s**t happens” category. These are the kind that are snakes in the grass, waiting to bite whomever happens to be the next unlucky soul to put a hand on the customer’s car. Stuff like a Chrysler’s oil dipstick that snaps off in your hand when you simply try to pull it out of the dip-stick tube. Or the earlier, Toyota canister filter caps made out of plastic that tended to shed their tabs when trying to remove them, even with the proper tool. The more experienced and more prepared you are for these individual circumstances, the more likely you will be able to recognize them beforehand, inform the customer of the situation and take appropriate care. But, even that doesn’t guarantee claims won’t bite you.
As a shop manager or owner, be aware of each vehicle in your bays at all times. When you see a potential problem vehicle in your bays, be sure to alert every team member working on that vehicle to any situation that may present a potential trap for them to fall victim to.
How about any of the later-model Nissan vehicles with TPMS? It is very common for corrosion to degrade the tire valve stem quite rapidly, even on a low-mileage vehicle. Attempting to remove the valve stem cap on such an afflicted tire stem can easily cause the stem to simply snap off, losing all the tire pressure and leaving a vehicle with a flat tire in your bays.
Of course, the customer’s attitude is, “Well, it wasn’t like that when I drove in here, so you have to pay to fix it.” Which, of course you do. Your shop was the last one to touch it, which gives you the hot potato.
In this situation, you not only lose the expense involved with paying a claim that was no fault of anyone in the shop, but you also risk losing a customer. On top of that, you have to suffer the bottleneck of business in your shop during the time it takes to get that situation fully under control. This causes you to lose not only potential sales as result from the tension and confusion, but also the loss associated with a slowdown in production for however long it takes to get back to smooth operations. The kicker to this is all the other customers who were there at the time may not be fully aware of the entire situation and you end up with a potential loss of repeat business from those customers, too.
Cascade Failures
These types of claims are usually the result of what I call, cascade failures. Like a row of dominoes all set up to fall one after another, it all starts with the first domino. If the first domino in line is not pushed over, the sequential chain of events does not take place.
How about a later-model GM full-size truck/ SUV with the 5.3L engine? There is nothing inherently wrong with these vehicles as far as an oil change is concerned, but they are ripe for a couple of different cascade failures. I am sure many of you know of these already.
First, and most direct, is the proper oil filter. This particular engine was manufactured in a couple of different engine plants, and the proper oil filter application is dependent on which plant manufactured it. The failure here is to accidentally improperly identify which engine is actually in the vehicle. Your POS system only knows what you input into it, and if you incorrectly identify the engine, then your work order will simply give you the wrong oil filter application.
Whoever relies on that work order will likely assume it is correct and will not be likely to notice an incorrect application. This type of cascade failure is stopped at the first domino — the identification of the correct engine — so the last domino — the failure of the engine due to an incorrect oil filter application — is prevented.
Another “gotcha” situation on this particular engine is the placement of the oil filter. It is nestled in safe and secure, right next to the oil pan in a half-moon shaped depression of the oil pan itself. It is easy to see and to get to and certainly looks like there should be absolutely no trouble with it.
The trouble is, when installing the new oil filter, there is not a sufficient amount of room to grip the filter to tighten it down securely.
Most oil filters require one-quarter to one-half a turn once the gasket makes contact, and that can be accomplished by hand in most circumstances with a straight shot at the filter. However, a tool must be used on this filter to get an adequate grip on it to tighten it, otherwise you will have a customer coming back for oil leaks — or worse. I have never been a fan of putting tools on a new oil filter unless absolutely necessary. On this one it is absolutely necessary.
When I see these vehicles in any of my shops, I always personally remind whoever is working lower bay on them that the filter is to be installed using a filter-cup. Hand-tight is never tight enough.
Low-Hanging Fruit
Another method to avoid claims is to follow the low-hanging fruit theory. It is actually quite simple to understand:
Imagine you decide to go collect some fresh oranges from the orange groves in your neighborhood, assuming you have permission. As you approach the orange tree with your bushel-basket, you see the tree is magnificently full of beautiful ready-to-be-picked oranges, top to bottom. The first branches are about five feet off the ground, and the tree is a good 20 feet tall overall.
Now, will you climb to the very top of the tree to start collecting your first basket of oranges? Probably not, there are plenty of oranges at the bottom for you to pick first. Simply, reach up and grab them. No ladder, no bucket-truck or cherry picker basket needed. There is plenty of low hanging fruit for you to grab and fill up a couple baskets before you even need to consider going after the higher, and more difficult to reach oranges.
If you can get all the oranges you need or want from the low-hanging sections, you never need to go on to the more-difficult-to-reach branches.
Now, if you do go after the higher branches you impose a couple of additional risks on yourself. However you get up there, you could suffer an unintended fall from 10 or 15 feet above the ground. It is unlikely you would fall from standing on the ground, but if you did, it certainly would not be the same as falling off a ladder or out of a tree.
In your shops, you should practice the low-hanging fruit theory and stay away from the more problematic and potentially more claim-likely situations. Even today, with all the extended mileage and longer maintenance intervals for other systems, there is still an abundance of low-hanging fruit — extra sales opportunities on the bulk of the vehicles coming in to your shop.
Difficult-to-reach fuel filters, automatic transmissions with no dipsticks and difficult-to-reach serpentine belts are just problems waiting to happen. Not only do they have the strong possibility of taking far longer than you initially thought, once finished you may have lost other business due to longer wait times. Of course, an unforeseen issue that happens on a situation resulting in a possible claim is only magnified by its factor of difficulty in the first place.
Have faith in your customers and in your ability to suggest the services they need on every vehicle, and you will be presented with enough low-hanging fruit during your day that you will never have to rely on those potential gotcha situations.
Make your day as easy as you can, and always, make it happen.
See ya next month!
About the Author
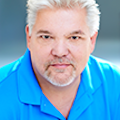