There is no doubt that today’s high-technology car and truck engines are becoming more and more sophisticated every year. Direct injection is the latest buzz term in the vernacular of new-tech power plants. You may have seen it identified by the letters GDI, which stands for Gasoline Direct Injection.
Every new and sophisticated technology introduced on modern engines delivers major improvements in performance, durability and economy, yet demands a higher level of internal engine cleanliness to maintain sophisticated performance.
Let’s take a brief look at the history of fuel delivery systems on typical engines and see what has changed in the engines themselves, as well as what has changed in the maintenance required to keep them running at peak performance.
The Stone Age: Carburetors
Not really the Stone Age, but carburetors seem so yesterday to most people today; mechanics as well as non-mechanical types.
The carburetor was actually a marvel of early mechanical design and function. Basically, the carburetor’s function was to properly mix gasoline and air in the ratio required. Through the use of an engine vacuum, it would deliver that mixed combo into the engine for proper combustion.
A carburetor sat on top of the intake manifold, and the mixed air and gas combination would flow through the intake manifold, down every cylinder runner and into the single cylinder that needed fuel for that particular combustion cycle, as well as every other cylinder that did not need it for that cycle. Of course, this was wasteful.
But, carburetors were nonetheless dependable, durable and worked well for years. Around the mid-1980s, Environmental Protection Agency (EPA) requirements began to get so stringent that it became increasingly difficult for car manufacturers to meet them using carburetor technology. Fuel injection was on the horizon, but the technology was expensive and manufacturers wanted to keep using carburetors as long as possible to circumvent that cost differential. All the major manufacturers made heroic efforts to continually modify and alter their carburetor design to help them meet those regulations, but they were all eventually forced to abandon carburetor technology and adopt fuel injection technology.
Central Fuel Injection
The first fuel injection systems used a set-up that could almost be described as a modified carburetor. A single (or maybe a dual) fuel injector was placed inside the throat of the throttle body, which almost perfectly resembled a carburetor, minus the vacuum-inducing venturi design of the throttle bore. Instead of using a vacuum to draw the fuel into the intake stream of air, the fuel injectors would mechanically squirt the fuel into the air stream in measurements that were more precise than a vacuum-operated system could deliver. This provided smoother operation, better performance and overall economy.
Multi-Port Fuel Injection
Central Fuel Injection (CFI) quickly gave way to Multi-Port Fuel Injection (MPFI), a dramatic advancement in fuel delivery technology. Instead of a single or dual injector feeding the engine from upstream at the mouth of the throttle body, MPFI placed an individual injector downstream in the manifold, very close to the backside of each intake valve. Depending on the engine configuration, there were typically four, six or eight injectors per engine. As air was just about to enter the cylinder past the intake valve, the injector would fire and fuel would be mixed and carried into the cylinder right at the intake port. Again, this resulted in a marked improvement in performance and fuel economy.
Sequential Multi-Port Fuel Injection (SMPFI)
This is where things really took a dramatic turn for improvement. While the physical set-up remained as before, new computer technology allowed the engines Central Processing Unit (CPU) to fire the individual injectors only at the time needed for each cylinder on the intake stroke. This prevented the wasted fuel from being delivered to the cylinders that did not need fuel on that particular stroke.
Fuel economy and overall performance were dramatically improved by this advancement in fuel injection.
However, a problem soon occurred. It was one that engine designers were unaware would happen. The PCV system routes unburned oil and gasoline vapors back through the intake manifold, past the intake valves and back into the cylinders to re-burn them during normal operation. In the early carbureted, as well as the CFI- and MPFI-injected engines, unburned fuel was continually running through the entire intake system, being wasted. However, the fuel that was washing through the intake manifold and past the intake valves had the tendency to keep them clean from oily residue and deposits resulting from the PCV operation.
As soon as the SMPFI came on line, the law of unintended circumstances took effect, and problems arose quickly that no one could have foreseen.
Remember, the sequential aspect of the SMPFI system delivers fuel only to the cylinder that needs it on that stroke. The other cylinders are only having air passed through them at this time — but not clean air.
Since there wasn’t wasted excess fuel running through all the time, these oily vapors tended to build up quite rapidly on the backs of the intake valves, dramatically affecting their ability to provide a proper compression seal. The result was the rapid onset of serious drivability issues, and the manufacturers were caught off guard.
The first method developed to clean the excessively dirty intake valves without removing the cylinder heads came from the use of crushed and pulverized walnut and pecan shells being injected into the engine while it was running.
This was akin to sandblasting the valves while still in the engine. The powdered walnut shells were abrasive enough to clean the valves but not so abrasive as to cause damage to other internal engine components. They would just work their way through the engine and out the exhaust.
This worked marvelously except for two factors: It was extremely labor-intensive, and it was a very expensive service to perform.
Intake Cleaning Solution
A need was recognized, and soon new and sophisticated chemicals designed expressly for cleaning intake systems and dirty intake valves were developed. Typically, these are delivered into the engine’s intake vacuum system while the engine is running at a high idle. This cleaning chemical is misted into the vacuum steam. It works its way in and through the engine and cleans the intake valves, the pistons and the intake system as it takes its journey through the engine.
Most lube shops across the country have been offering this as a two-part or three-part intake cleaning service for years. It is a vital and necessary service to perform on today’s modern engines.
Gasoline Direct Injection (GDI)
Now, with the latest and greatest advancement in fuel injection technology, comes direct injection. The main difference is that GDI places the fuel injector tip inside the combustion chamber, which allows all kinds of great stuff.
Smaller engines can be made with higher compression ratios without fear of early fuel detonation or pre-ignition. This allows a dramatically increased power output from a smaller engine. The GDI also allows the use of lower-octane fuels in the high-compression engine, saving the driver money at the pump.
However, since all the fuel is now being delivered directly into the cylinder, well down-stream of the intake manifold and the back of the intake valves, there is not even a modicum of fuel washing past the intake valves to help keep them clean.
The result is an astoundingly rapid build-up of sludge and carbon deposits on the intake valves and in the intake tract, delivered there by the PCV system, which is continually running that nasty, oily residue through the intake system.
The hot and dry intake valves are quickly caked with residue, which builds up rapidly.
A secondary negative effect of this is that this carbon can also quickly build up on piston rings, compromising compression sealing. This results in rapid and excessive combustion blow-by past the rings, polluting the engine’s motor oil with dirty combustion by-products.
If you look at the oil in any typical modern GDI engine when it comes into your shop for an oil change, don’t be surprised to find excessively dirty and black oil on the dipstick after only a normal oil change interval.
Here’s Your Opportunity to Help Your Customers
Never before has it been as critical to maintain a clean intake system as it is on modern GDI vehicles, and never before have they “sludged” up as quickly as the modern GDI engines do.
A dirty or poorly maintained GDI engine will suffer severe drivability issues very rapidly if the intake system is not cleaned regularly and often.
A general recommendation of every 15,000 miles or once a year is a reasonable recommendation for you to perform a multi-stage intake cleaning service on your customer’s GDI vehicles.
Your chemical vendors will be happy to verify this information about their intake-cleaning systems for you, and the top-line vendors will even come to your facility to teach you and your employees all about the service. They may even provide some pizza and sodas for your crew!
KIT SULLIVAN is a partner in a multi-unit, Florida-based quick lube company. A 20-year veteran of the industry, Sullivan has more than 28 years experience in sales and management training. He is a member of the Society of Automotive Engineers and the Society of Tribologists and Lubrication Engineers. He can be reached via email: [email protected]
About the Author
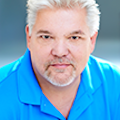